在铠装电缆的护套挤塑生产时,由于缆芯自重原因,在缆芯过模过程中缆芯外层钢带会与模芯内壁接触,缆芯外层钢带会带走部分热量,且因都是金属物之间接触,导致传热速度快,从而使模芯内壁(模芯承径段)温度下降,导致护套料挤塑过程中容易出现塑化不良、皱皮、偏芯或脱料现象。且随着环境温度的下降,表面塑化不良质量缺陷越明显,直接影响铠装电缆的产品质量。
(一)未改进前生产状况描述
为了减少铠装电缆的护套挤塑生产时缆芯外层钢带会模芯内壁接触,尽量使缆芯从中心位置进入机头模芯:入模口处约400mm有一个支持缆芯导轮,整个机头总长约560mm,机头与水槽中第一个导轮间距有1米多,现有挤塑模芯是通孔,但由于缆芯自重的因素,很难保证缆芯挤塑时处于悬空状态,从而缆芯在进模处会与模芯内壁接触,且电缆外径越大,铠装与模芯的接触面积越大,传热越严重,导致挤塑模口处温度低于材料的塑化温度,在电缆的表面形成连续的塑化不良硬包、偏芯、皱皮等。
(二)改进后解决的技术问题
1、在挤塑模芯承径段上距挤塑模外端25mm处设置一个高为1mm,倾斜角度为30°的台阶段,以减少铠装层与模芯内壁的接触面积,从而减少钢带带走的热量;
2、增大挤塑模套的内径(模芯外径与模套内径配模比值由原来的标称厚度的3.5倍调整到5倍),以增大挤塑模承径段塑料的热惯量。
通过以上两点的改进,确保铠装电缆护套挤塑时模口温度不低于材料的塑化温度,从而彻底解决铠装电缆护套挤塑生产时因钢带传热导致的塑化不良、皱皮、偏芯或脱料等质量缺陷。
(三)生产过程示意图
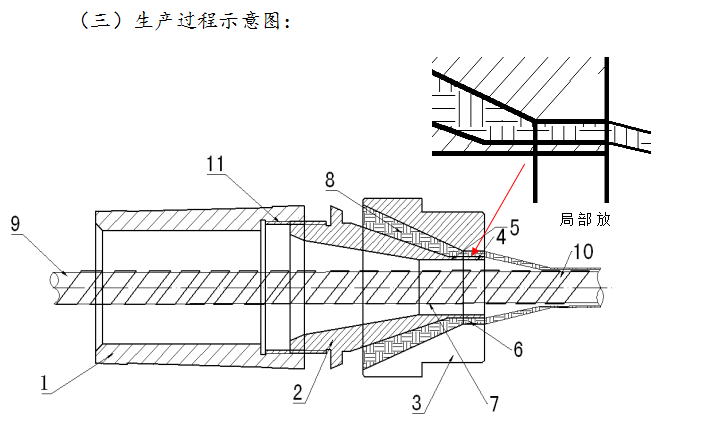
修改前加工示意图
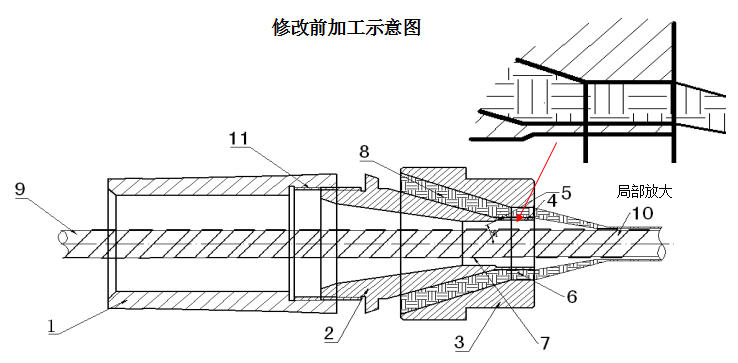
修改后加工示意图
1、模芯座 2、挤塑模芯 3、挤塑模套 4、模芯定径区 5、模芯嘴内壁30° 斜角台阶 6、模套定径区 7、缆芯双层间隙绕包钢带铠装层 8、模芯与模套间填充的挤塑材料 9、缆芯进线 10、挤塑完成后的成品电缆 11、模芯座与模套的连接部位
(四)对挤塑过程说明
1、生产过程示意图中是电缆在挤塑过程中理论进线,在实际生产中操作人员能确保进线在中轴线位置,由于电缆的自重以及进线到出线的悬空造成电缆出线会偏下紧贴模芯内壁。
2、模芯定径区总长为45mm, 模芯嘴内壁30°台阶设置在离模芯外端25mm。
3、生产时模芯座尾端会加增加支持导轮装置,将电缆过线位置与中机头的中心位置保持一致。
4、增加的30°1mm台阶位置,将电缆的进线在25mm处抬高垫,使电缆的铠装多属层与模芯有间隙,保持挤出塑料的塑化不良问题。
(五)模芯示意图
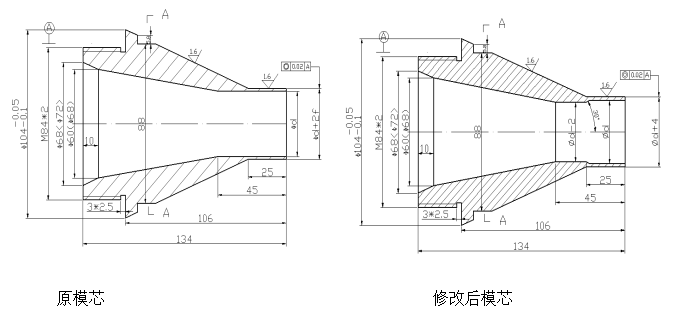
(六)有益效果通过对挤塑模芯的内部结构进行调整及放大模套内径与模芯外径的差值,有效地解决了铠装电缆护套挤塑生产时因钢带传热导致的塑化不良、皱皮、偏芯或脱料等质量缺陷,提高了金属层铠装电缆护套挤塑表面质量,降低环境温度过低对挤塑表面的影响。 (李渊峰 潘春梅) |